Energy and Environment
Automation, innovation and enclosed zones combine to create process improvements to deliver a range of recycling benefits, reduce the emissions generated by traditional galvanizing and improve safety throughout the different processing zones of a galvanizing plant. KTE can design these factors into galvanizing plants which ensures plants are both productive and environmentally responsible.


Energy Use
Substantial energy is required to heat the hot dip galvanizing bath and pre-treatment tanks. Although galvanizing is not considered to be amongst the most energy-intensive sectors of industry it is none the less a critical cost component for all galvanizing plants. Energy is expensive and will continue to become more costly and galvanizing plants need to be designed or updated with this in mind. It is critical for the profitable operation of a galvanizing plant that energy is used efficiently – and re-used wherever possible. KTE understands these requirements and that the galvanizing industry has set targets for energy efficiency and encouraged improved energy management and new technology to achieve these targets.
KTE provides:
- improved burner technology for greater energy efficiency
- improved infinite control over the burners through advanced PLC programming technology
- improved insulation techniques and materials
- more efficient bath enclosures
- greater use of waste heat for heating of pre-treatment tanks
KTE is a leader in combustion technologies designed to achieve maximum performance whilst minimising energy use. Our Control Systems have been designed and built specifically to achieve this and provide global leading results.
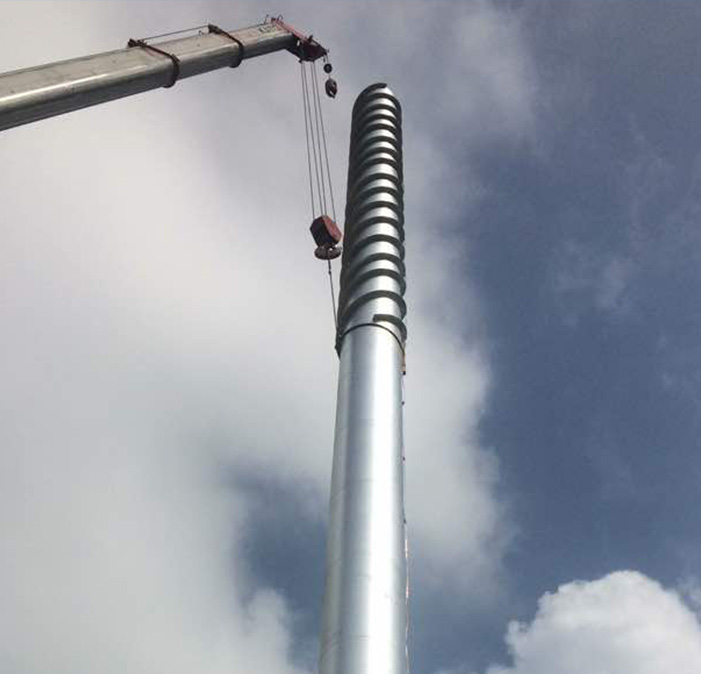
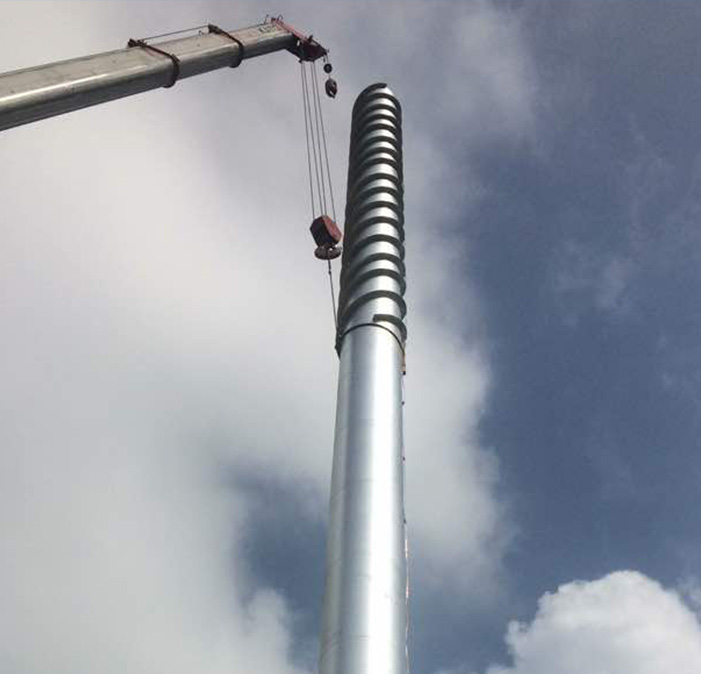
Emission Control
The control of emissions is becoming an increasingly important consideration in the design and operation of galvanizing plants. Emissions need to be carefully controlled to avoid contamination in the surrounding neighbourhood, in the land holding and to comply with ever increasing government regulations.
Kingfield Technology & Equipment factors emission control to suit local conditions into all Galvanizing Plant designs.
Sustainability
KTE can design into plants the use of automated materials handling systems to deliver greater processing consistency, therefore reducing consumption of chemicals and waste production. A focus on sustainability in designing innovative systems helps reduce emissions, increase recycling, re-use outputs to minimise waste, improve workplace safety and create a cleaner working environment.
In addition, The Reclaimer King Furnace is designed to reclaim metal from the ash that is created by skimming molten metal and impurities in bath type applications such as galvanizing. This process results in cost savings and improved productivity by managing the process on site. Please refer to the detail about the Reclaimer King under equipment.